How Extrusion Technology Revolutionizes Precast Concrete Slab Manufacturing
Precast concrete slabs are fundamental components in modern construction, offering efficiency, durability, and design flexibility. Central to their production is extrusion machinery – a cornerstone of advanced precast concrete manufacturing equipment. This article demystifies the working principles of extrusion-based slab production.
1. Core Equipment: The Precast Concrete Extruder Machine
Extruders belong to the category of prekast beton maki̇neleri̇ designed for continuous, high-output slab formation. Key components include:
- Steel Strand Guidance System: High-tensile steel strands are tensioned along the casting bed as reinforcement skeletons, ensuring structural integrity.
- Auger Conveyor & Hopper: Pre-mixed concrete is fed into the hopper, where rotating augers force material through a shaping mold with controlled density.
- Integrated Vibration Plate: High-frequency vibrators compact concrete, eliminating air pockets and achieving optimal density.
2. Step-by-Step Manufacturing Process
(1) Pre-Tensioning Reinforcement
Use a hydraulic tensioning machine to tension the steel bars or steel strands to increase the bearing capacity of the floor slab.Steel strands are stretched to 70-80% of their ultimate strength and anchored at the bed ends, creating a pre-stressed framework for load-bearing capacity.
(2) Concrete Extrusion & Molding
- Concrete is pumped into the extruder’s hopper.
- The auger system pushes material through a profiled mold, forming the slab’s cross-section (e.g., hollow cores, ribbed surfaces).
- Simultaneous vibration compacts the mix, ensuring homogeneity and surface smoothness.
(3) Curing & Demolding - Slabs remain on the casting bed for 12-24 hours of steam curing to accelerate strength gain.
- Once cured, strands are released, transferring compressive stress to the concrete.
- Slabs are cut to specified lengths (4m–18m) using diamond-tipped saws.
3. Technical Advantages of Extrusion Machinery
Feature | Benefit |
---|---|
Continuous Operation | Output speeds of 1.3–1.5 meters/minute enable mass production. |
Hassas Kalıplama | Customizable molds create consistent cross-sections (±2mm dimensional tolerance). |
Enerji Verimliliği | 380V power systems with ≤4.5kW consumption reduce operational costs. |
4. Applications in Modern Construction
Extruded slabs are ideal for:
- High-Rise Buildings: Hollow-core slabs reduce weight while maintaining strength.
- Endüstriyel Tesisler: Rapid production supports large-scale projects.
- Sustainable Design: Optimized material usage minimizes waste.
Sonuç
Extrusion-based precast concrete manufacturing equipment represents the synergy of mechanical innovation and material science. By integrating tensioning, vibration, and continuous molding, prekast beton maki̇neleri̇ like the KELAI extruder delivers structural components that redefine construction efficiency. As modular building gains traction, this technology will remain pivotal in shaping resilient infrastructure globally.
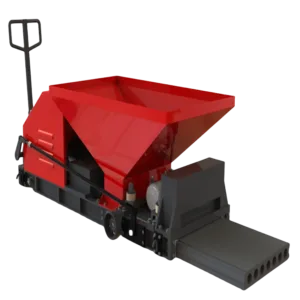