How can precast concrete slab manufacturers produce precast concrete panels efficiently?
Precast Concrete Hollow Core Slab is commonly used in big buildings, factories, and homes. It is lightweight, strong, and easy to build with. As a maker of precast concrete slabs, choosing the right machine is important. Learning production techniques also helps. Both of these factors can improve efficiency and product quality. This article will explain how to use the Concrete Hollow Slab Forming Machine. It will cover equipment selection, the production process, key technical points, and industry trends for efficient production.
1. Core functions and selection suggestions of hollow slab forming machine
The precast concrete hollow slab machine makes strong and precise slabs. It uses a long-line table mold process and prestressed steel strand tensioning. The following are the key parameters and suggestions for equipment selection:
Equipment specifications:
Slab size range: length 4.2 meters to 18 meters, width 600mm to 1200mm, thickness 120mm to 380mm.
Power and production capacity: For example, the maximum load of the KELAI380-1200 model is 12.27 kN/m², and the production speed is 0.8-1.0 meters/minute.
Mold type: Circular and diamond hole designs can be selected to meet different structural requirements.
Selection suggestions:
Match equipment according to project requirements: If producing large-span slabs (such as 18 meters), a high-load model must be selected.
Focus on wear resistance and maintenance: It is preferred to use equipment with stainless steel hoppers and alloy wear-resistant parts to reduce long-term operating costs.
Technical support and after-sales service:
- Pick suppliers that provide free technical training.
- Ensure they offer a one-year warranty on the machine.
- Check if they have spare parts replacement services. Look for options like KELAI machines and other brands
2. Detailed explanation of the production process of precast concrete hollow slabs
Raw material preparation:
Concrete ratio: Cement, aggregates and additives need to be selected according to the strength requirements of the slab. Some equipment supports environmentally friendly materials such as fly ash and slag.
Prestressed steel strands: High-strength and low-relaxation steel strands (diameter 9.5mm or 12.7mm) are used to ensure the bending resistance of the slab.
Production steps:
Strand tensioning: Fix and tension the steel strands on the long line table to apply prestress.
Concrete pouring and molding: Fill the mold through extrusion or push-type processes, and form a hollow structure after vibration compaction.
Curing and cutting: Natural curing or steam accelerated curing, use a cutting machine to cut the slab as needed.
Quality control:
Regularly calibrate the equipment tension and mold size to avoid deformation or thickness deviation.
Detect the slump and density of concrete to ensure a smooth surface without pores.
3. Recommendations of leading manufacturers and equipment suppliers of precast concrete panels in the industry
Equipment suppliers:
Henan Kelai Industrial Co., Ltd : Focuses on extrusion molding technology, provides fully automatic production lines and overseas installation support, and exports to markets such as Africa, the Middle East, and Southeast Asia.
KELAI machine has a skilled team of Chinese engineers in the construction machinery field. They offer complete solutions. Their products cover 80% of the Chinese market and are sold in 65 countries.
Multi-platform supplier: Provides a variety of equipment models (such as the JQT series), supports customized molds and a full set of technical solutions.
Manufacturer cooperation suggestions:
Give priority to suppliers with ISO 9001 certification and more than 5 years of experience to ensure equipment stability.
Require suppliers to provide production process planning, localized material adaptation solutions and after-sales training services
4. Future trends and innovative technologies
Automation and intelligence:
Integrate PLC control systems and sensors to achieve real-time monitoring of tension and pouring speed.
Some equipment already supports remote fault diagnosis to reduce downtime.
Green production:
Use recycled aggregates and low-carbon cement to reduce carbon emissions.
Equipment energy consumption optimization (such as the JQT380 model has a power of only 39.2kW), in line with sustainable development needs
5. Conclusion
Precast concrete slab manufacturers can benefit from investing in advanced machines. These machines can boost production and improve product quality. They also allow for flexibility to meet different market needs with modular design. Choosing equipment suppliers that fit the skills of precast concrete slab makers is important. Continuously improving production processes will help companies stay ahead in the growing construction industry.
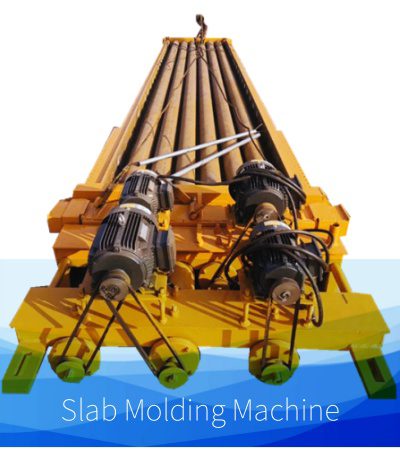
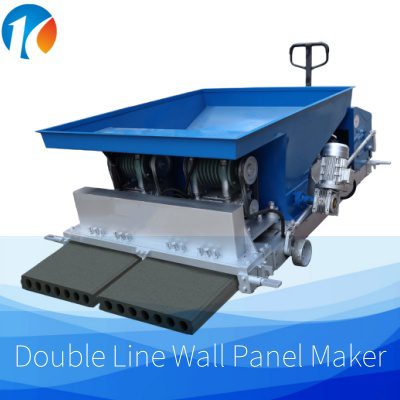