How Does a Lightweight Concrete Wall Panel Machine Work? Full Guide to Structure and Production Process
If you’re looking to understand how lightweight concrete wall panels are made, you first need to grasp the forming principles and working process of a lightweight concrete wall panel machine. These machines are essential in modern precast construction, enabling the mass production of durable yet easy-to-install wall systems used in residential, commercial, and industrial projects.
In this article, we will explore the complete structure, functionality, and advantages of the lightweight concrete wall panel machine, helping you better understand why it is a key piece of equipment in today’s construction industry.
1. What Is a Lightweight Concrete Wall Panel Machine?
A lightweight concrete wall panel machine is a highly specialized mechanical system used to produce partition boards or structural concrete panels with reduced weight, while maintaining excellent strength, insulation, and fire resistance. These machines are often used in large-scale housing projects, office buildings, and prefabricated modular structures.
2. Structural Composition of the Machine
2.1. Raw Material Processing System
This system is responsible for measuring, crushing, screening, and mixing raw materials such as cement, sand, ceramsite, fly ash, and lightweight aggregates like perlite or plant fiber. A precise metering device ensures that each component is weighed accurately, maintaining the correct mix ratio. This consistency is crucial for ensuring stable physical properties and achieving the desired lightweight effect in the final wall panels.
2.2. Mixing System
The mixed raw materials are delivered to a high-efficiency mixer where they are blended uniformly. Uniform mixing is vital because any inconsistency can lead to structural weaknesses. The mixing system is designed to maintain a consistent moisture and density profile across the batch, improving the overall durability and appearance of the panels.
2.3. Forming System – Spiral Extrusion & Vibration Compaction
This is the core part of the lightweight concrete wall panel machine. The forming system includes:
- Spiral Extruder: Driven by the main motor via a pulley and gearbox, the spiral reamer pushes the concrete mixture forward into the forming mold.
- Vibration Compaction: Simultaneously, high-frequency vibration ensures the mixture is fully compacted, eliminating bubbles and enhancing structural density.
- Self-Propulsion Mechanism: The reaction force generated during extrusion causes the machine to move linearly along the guide rail, allowing for continuous forming of panels.
Together, these mechanisms ensure that the panels are strong, dimensionally accurate, and resistant to cracking.
2.4. Molding and Surface Finishing
The mixture is shaped using hollow-core or solid molds, depending on the panel design. A surface scraping and smoothing device ensures that the panel surfaces are flat, aesthetically pleasing, and ready for installation or painting. Adjustable mold thicknesses allow for production of panels for different applications, such as load-bearing or non-load-bearing use.
2.5. Cutting and Packaging System
Once the panels have cured—typically under natural conditions—they are cut to the required dimensions using specialized cutting equipment. This stage ensures uniformity and compliance with construction site requirements. Finished panels are then stacked, wrapped, and prepared for transport or storage.
3. Advantages of Lightweight Concrete Wall Panel Machines
✅ High Production Efficiency
The machine supports fully or semi-automated production, dramatically increasing daily output. A well-configured production line can manufacture hundreds to thousands of square meters of panels per day, making it ideal for high-volume projects.
✅ Consistent Product Quality
Advanced metering and automation ensure every panel meets strict quality standards. Accurate control over raw material ratios and curing times leads to panels that are crack-resistant, moisture-proof, and structurally sound.
✅ Labor Saving
Automation reduces the need for skilled manual labor. Tasks such as feeding, forming, and even packaging can be automated, lowering labor costs and increasing workplace safety.
✅ Eco-Friendly Production
Many machines are designed to recycle leftover concrete and reduce dust or emissions. Additionally, lightweight panels help reduce the carbon footprint of transportation and on-site handling.
4. Applications of Lightweight Concrete Wall Panel Machines
These machines are widely used in:
- Prefabricated housing systems
- Interior and exterior partition walls
- Temporary construction walls
- Industrial and commercial buildings
- Public housing projects in developing regions
The versatility of the wall panels produced makes them suitable for both structural and decorative applications.
5. Conclusion
The lightweight concrete wall panel machine is a game-changing innovation for the construction industry, offering a fast, efficient, and cost-effective way to produce high-performance wall panels. Its advanced forming systems, automation capabilities, and scalability make it ideal for construction firms, precast factories, and entrepreneurs looking to expand into the prefab building materials sector.
If you’re considering investing in lightweight wall panel manufacturing equipment, be sure to assess machine specifications, production capacity, and automation level according to your project scale and market needs. The right machine can greatly enhance your productivity and product quality—putting you ahead in the growing precast construction market.
Concrete mixing plant equipment
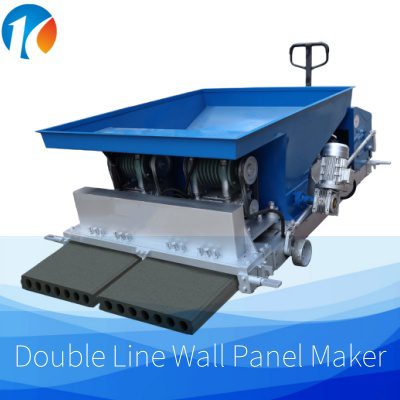